our history
140 years of growth
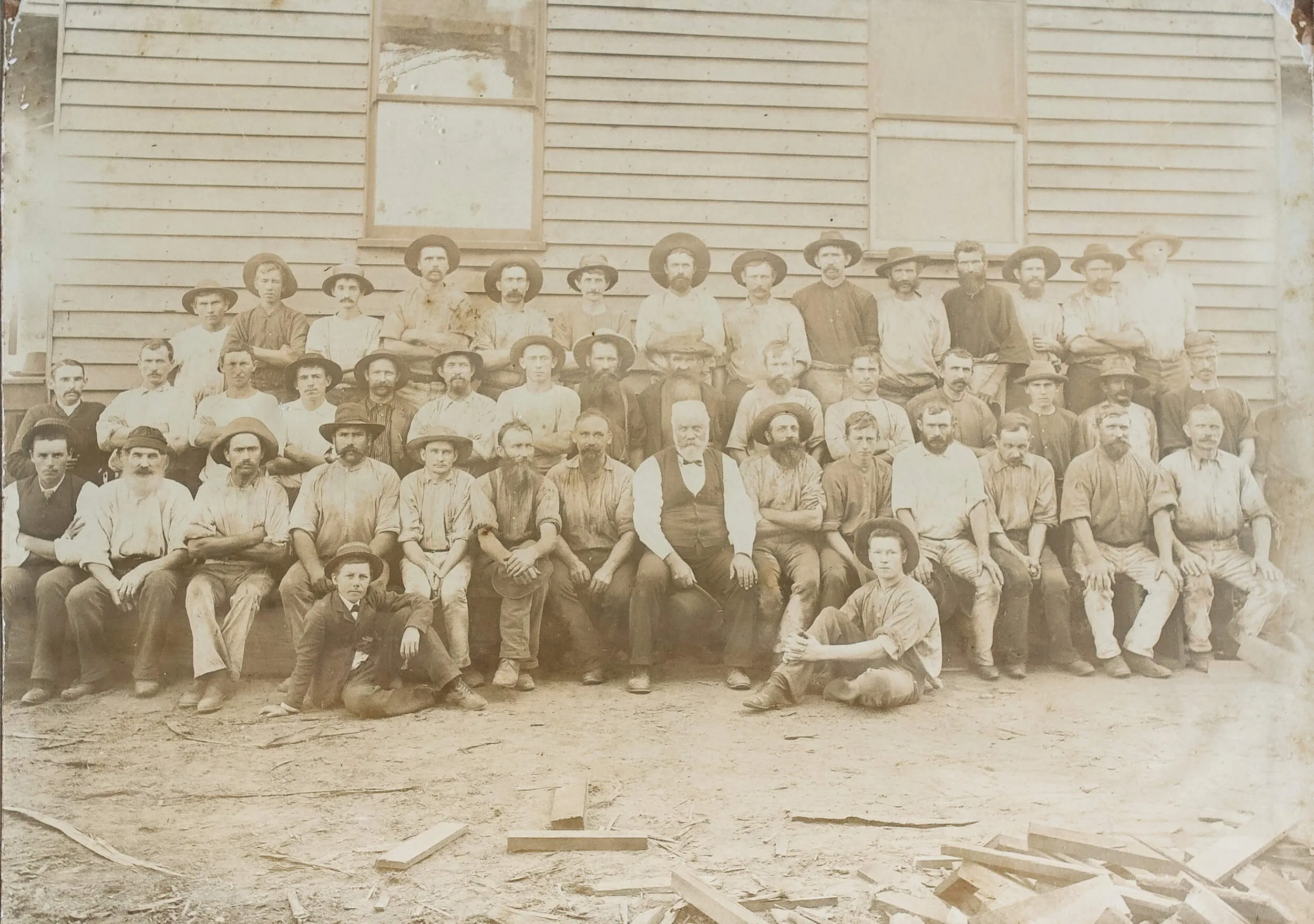
The key to our longevity
Hyne Timber is one of Australia’s largest producers of structural timber products, a leader in preservative treatments and an iconic supplier to the Australian construction industry. We also implement standards throughout our business that underpin our commitment to product quality, service, safety and sustainable timber production.
This is our story
Over the decades, Hyne Timber has helped shape the Australian timber industry with many bold innovations, all the while navigating floods, bushfires, wars, pandemics, depressions and recessions. Despite these challenges Hyne has not only survived, but has grown to become an industry leader.
1882
R.M. Hyne established The National Saw Mill on the banks of the Mary River.
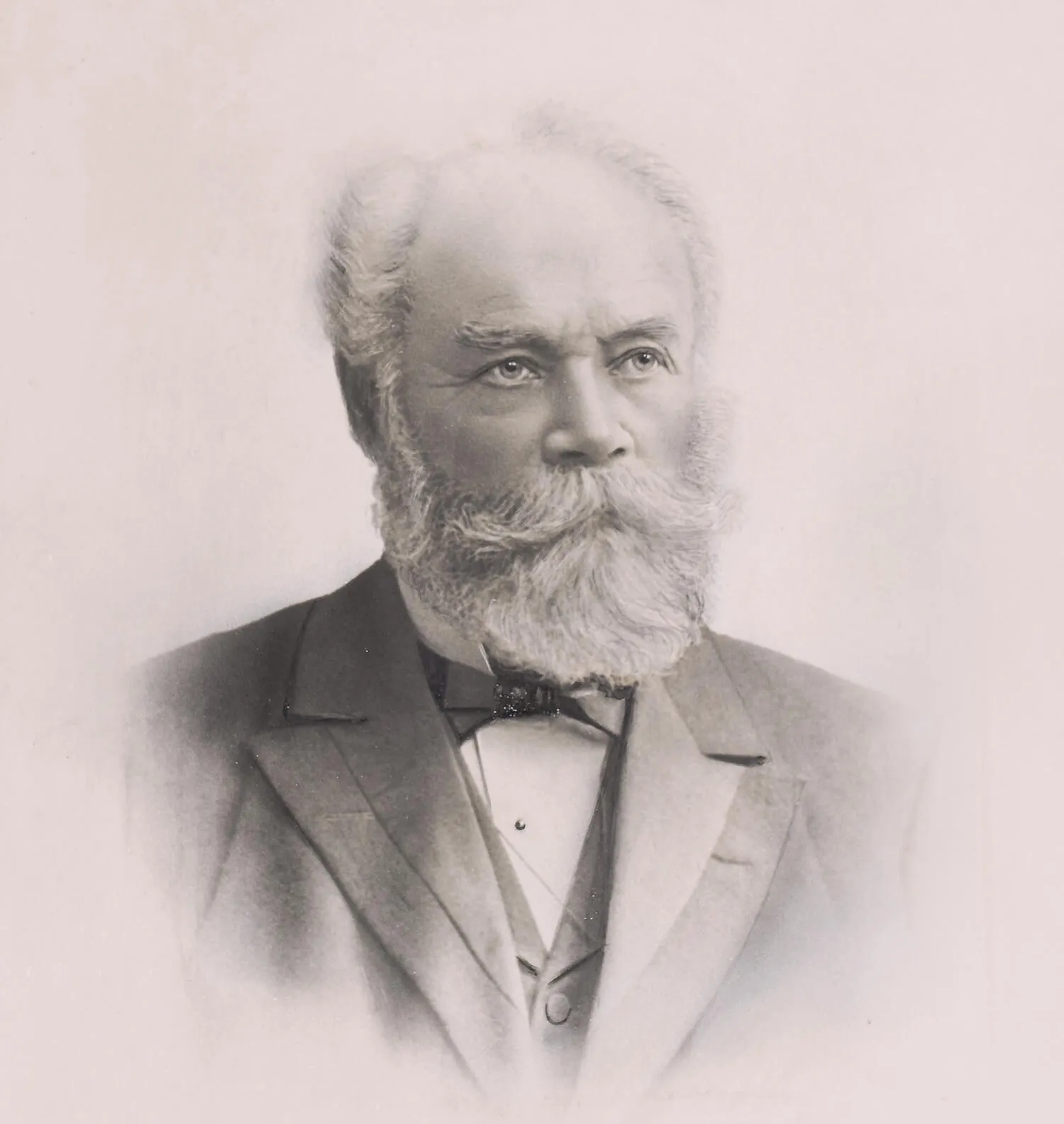
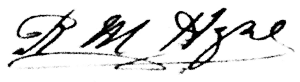
1880s — 90s
In 1886, Hyne purchased the Mayflower schooner, representing a turning point for the business as it could freight its own logs at a time when there were crippling freight costs. However, in 1893 the ‘The Great Flood’ hit Maryborough, the largest flood recorded in the Mary River at 12.27 metres. Hyne was one of the regions heaviest sufferers as the mill, buildings, stock were all swept out to sea without one penny of insurance.
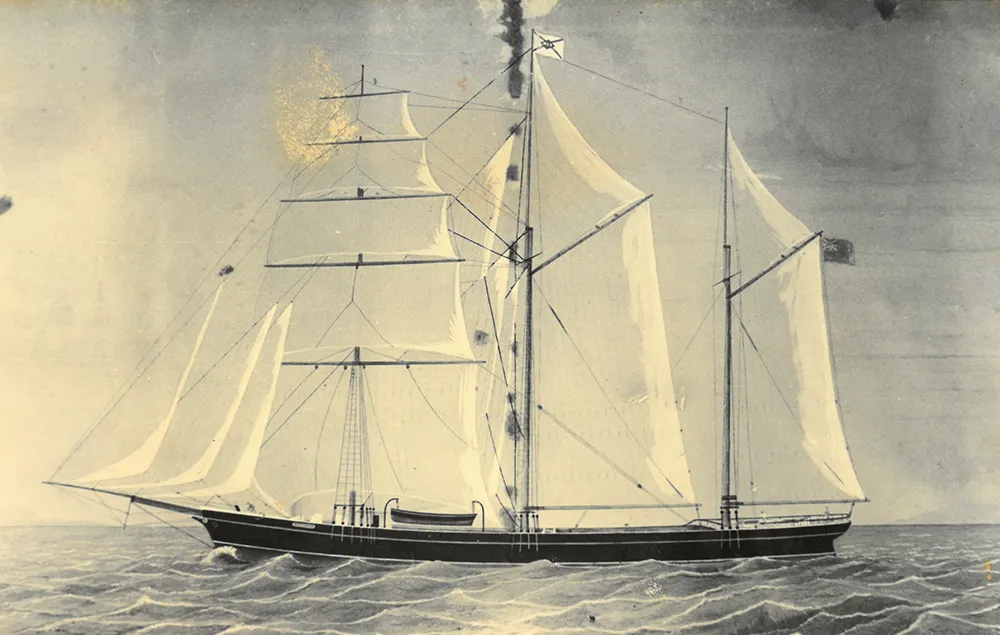
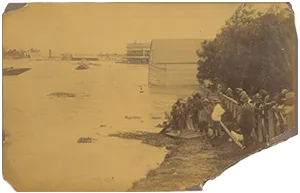
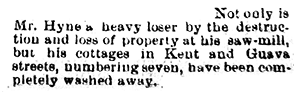
1900s
Having rebuilt on higher ground, R.M. passed control to his son Henry, who set about revolutionised local production with the addition of the modern band saw, commissioning a North American sawmill line, comprising of a steam engine, 8 foot band mill, edger and band resaw.
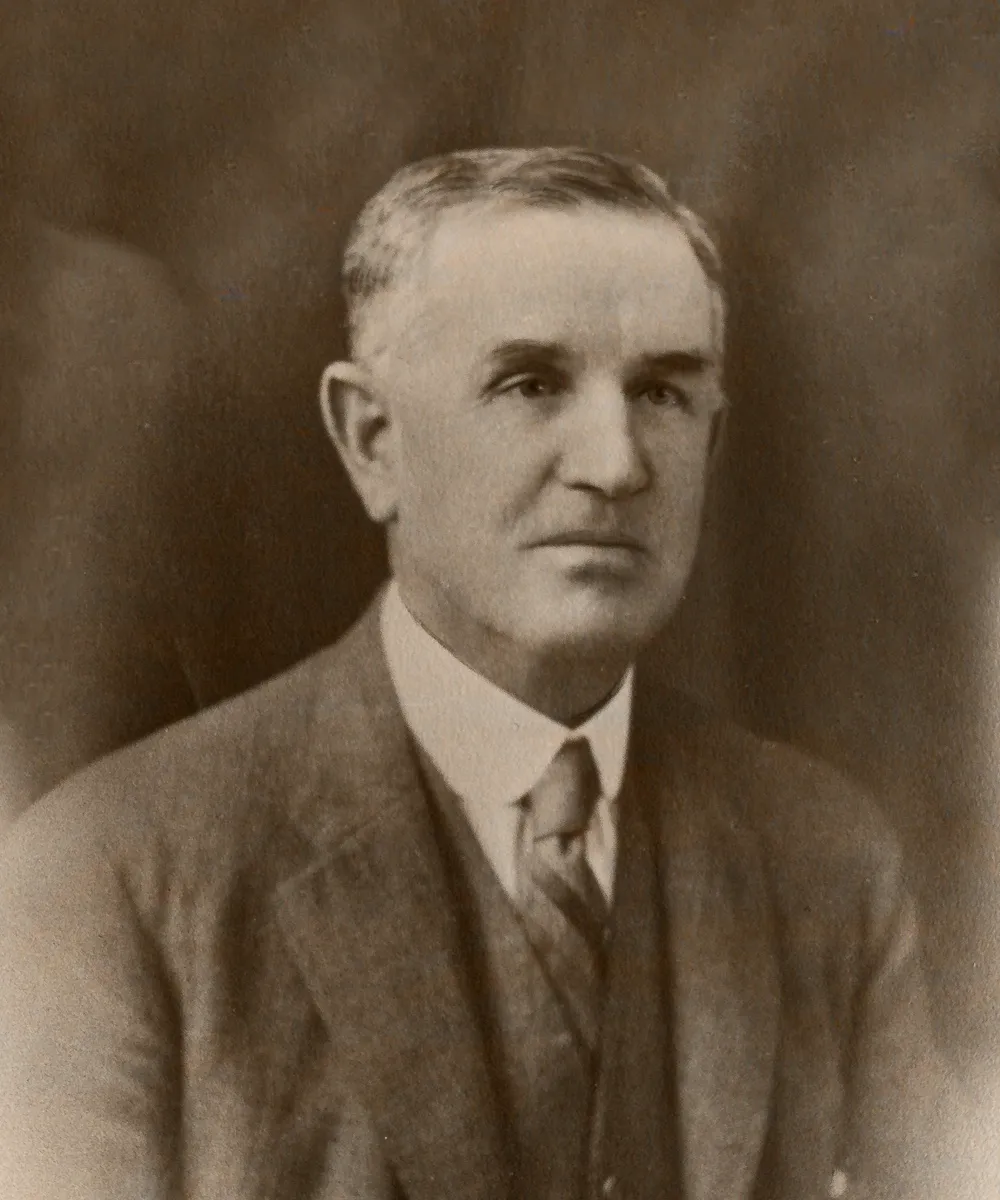
1930s — 40s
The 1930s saw a lack of timber demand, followed by over cutting of timber during WWII. During this time, Hyne implemented one of Australia’s first ever drying kilns.
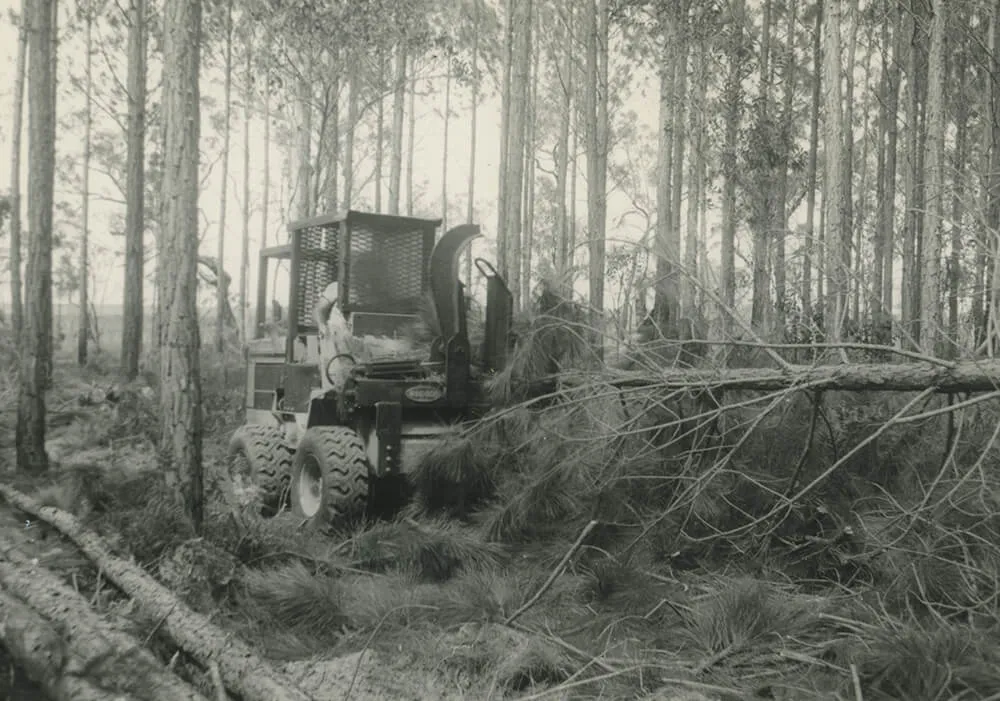
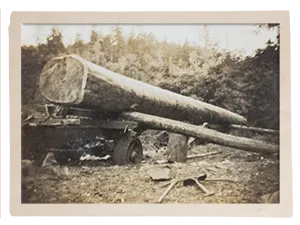
1950s — 60s
Hyne increased their stake in the pine plantation industry. In the 1960s Hyne drove the adoption of treated timber.
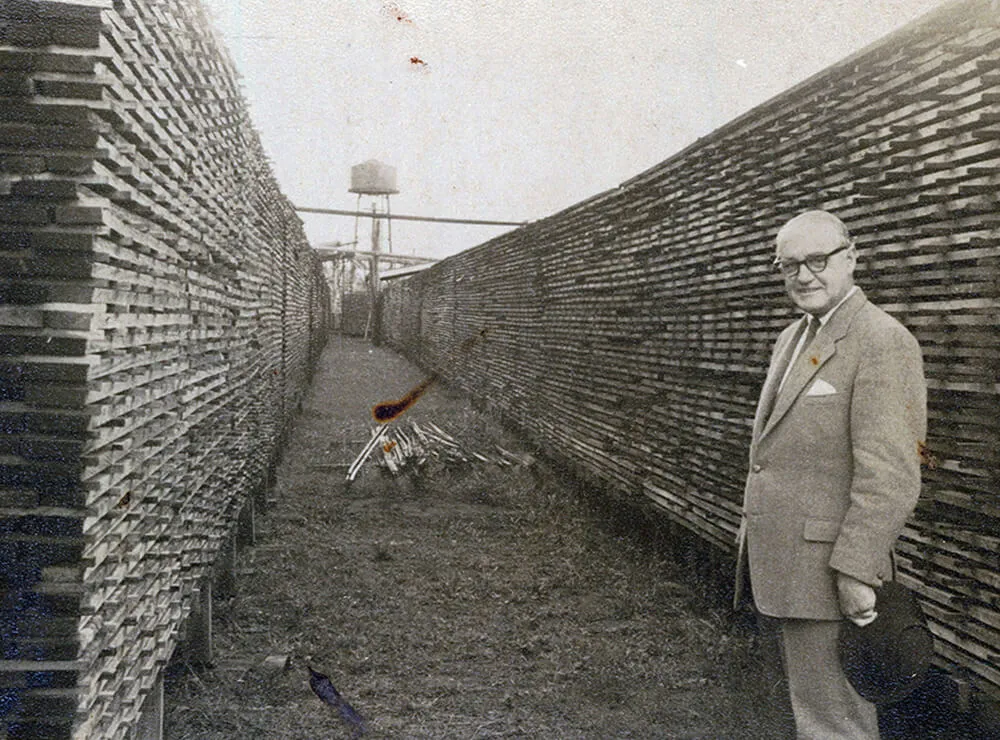
1978
“I realised that instead of just selling a commodity we should be selling a manufactured engineered product.” – Lambert Hyne, on shifting supply away from ‘round timbers.’
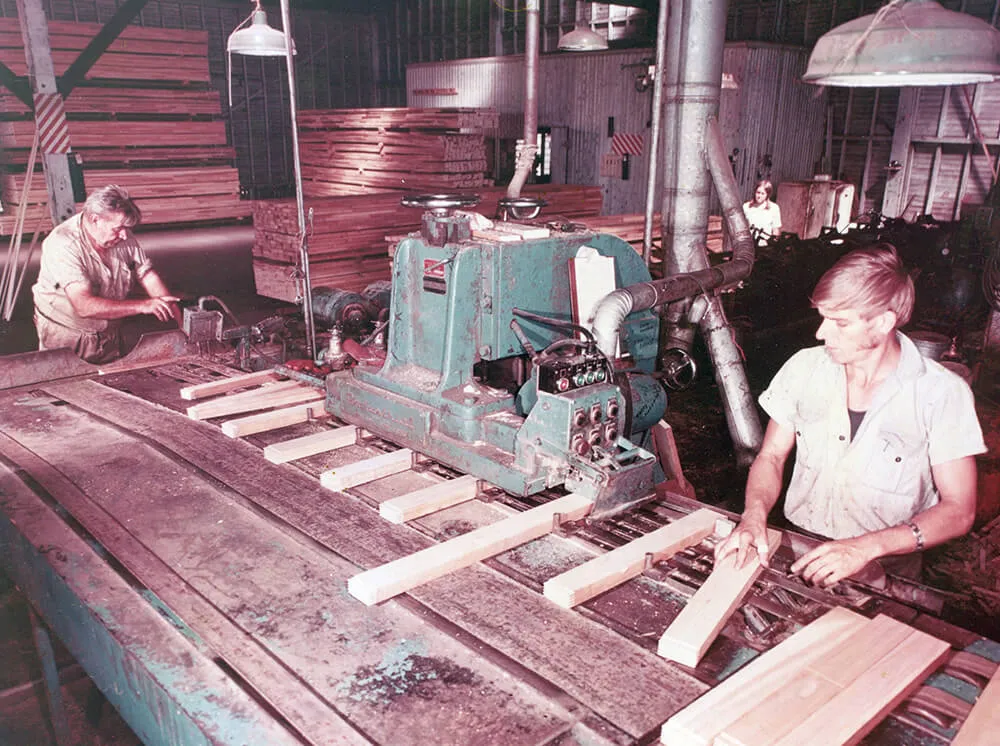
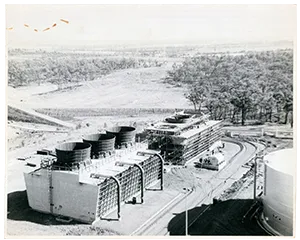
1980s — 90s
After 100 years, Hyne moved away from native hardwood. Led by Warren Hyne, R.M’s great grandson and respected captain of industry, the business transformed from small scale sawmills to high volume modern softwood processing. In 1986 Hyne built the Tuan Mill and began production of GLT, forging a future in engineered timber products.
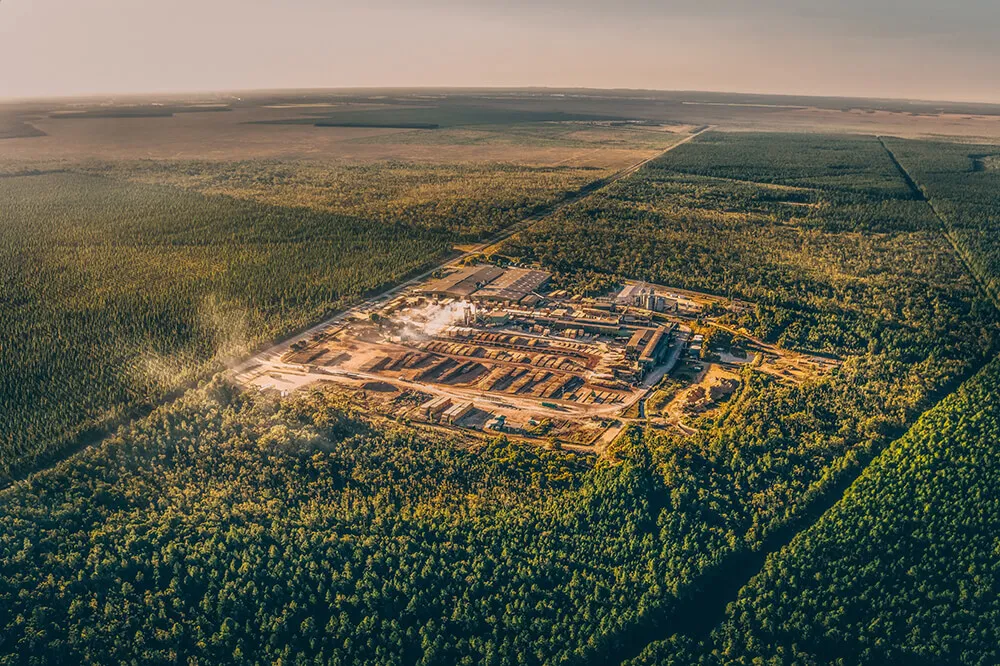
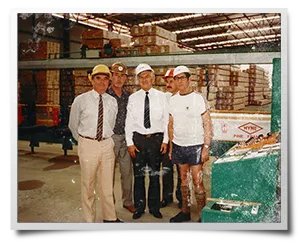
2000s
In 2001 Hyne expanded operations with the addition of the Tumbarumba Mill. In 2003 Hyne doubled down on sustainability with 100% renewable softwood. The early 2000s also saw Hyne introduce the blue dye into their treatment, setting a tone that others would soon follow.
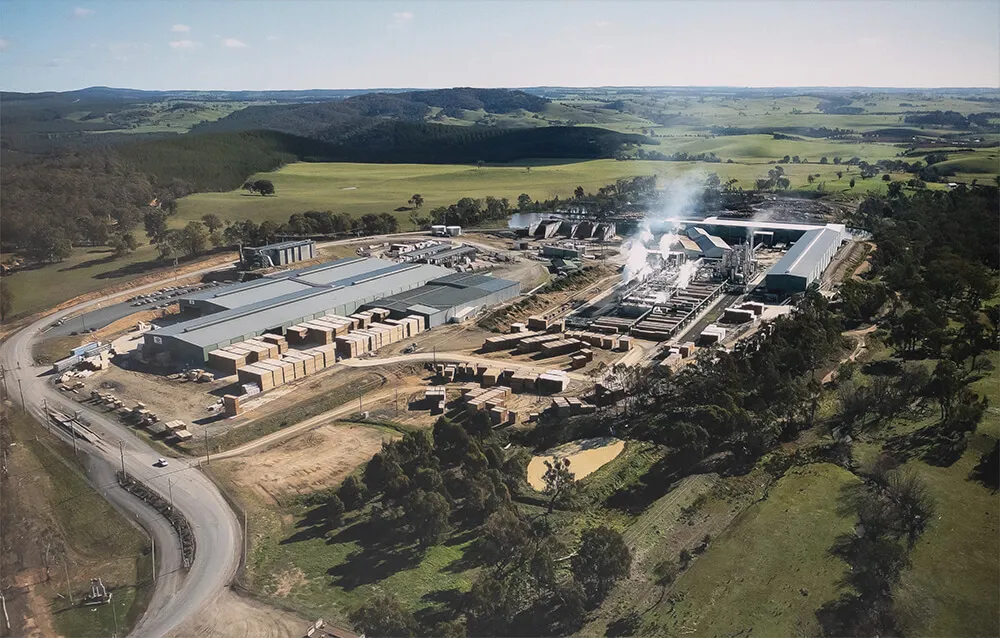
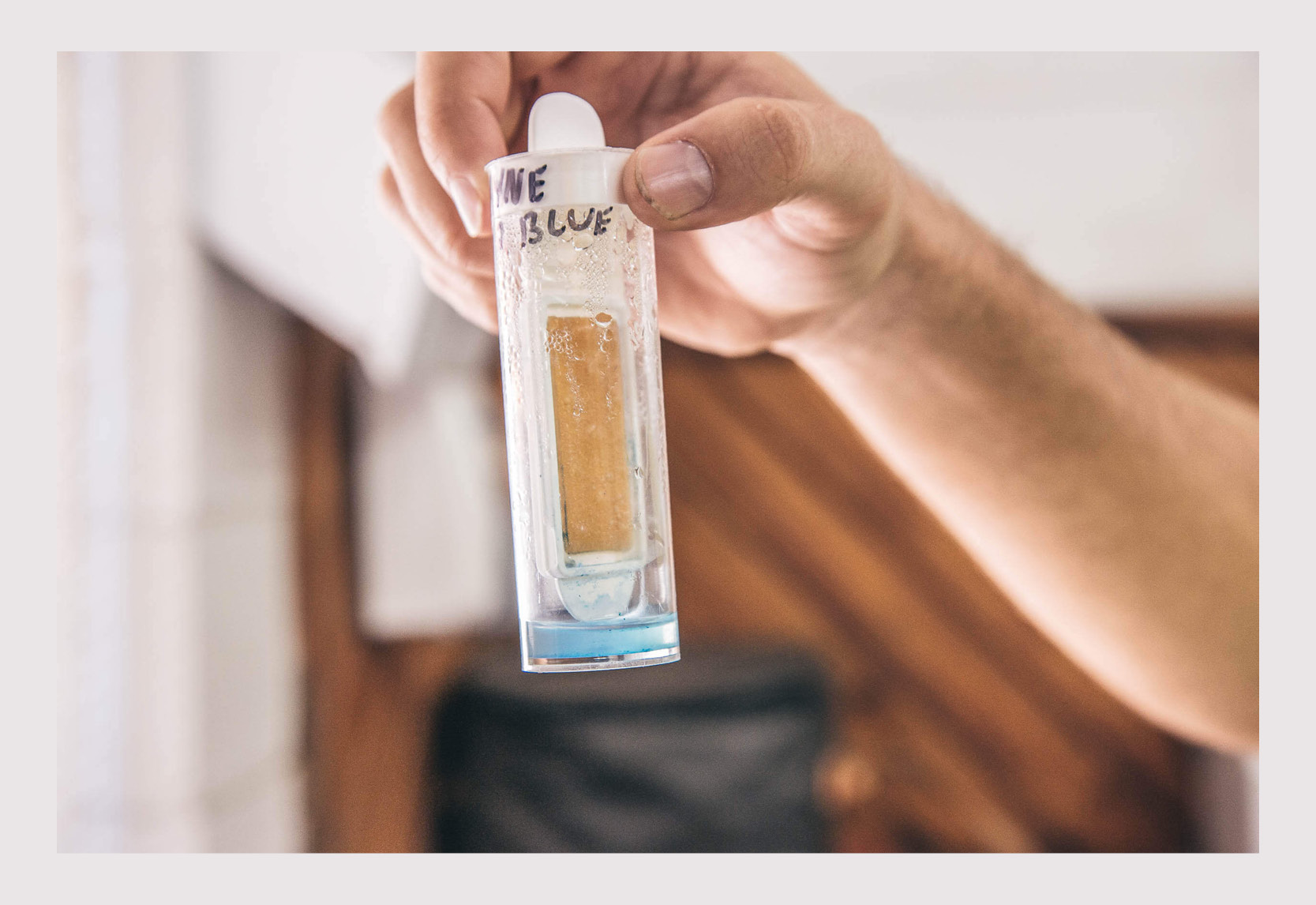
2015
With no other CLT competitors in Australia, the time was right for XLam to join the Hyne family and bring true mass engineered timber to an Australian market.
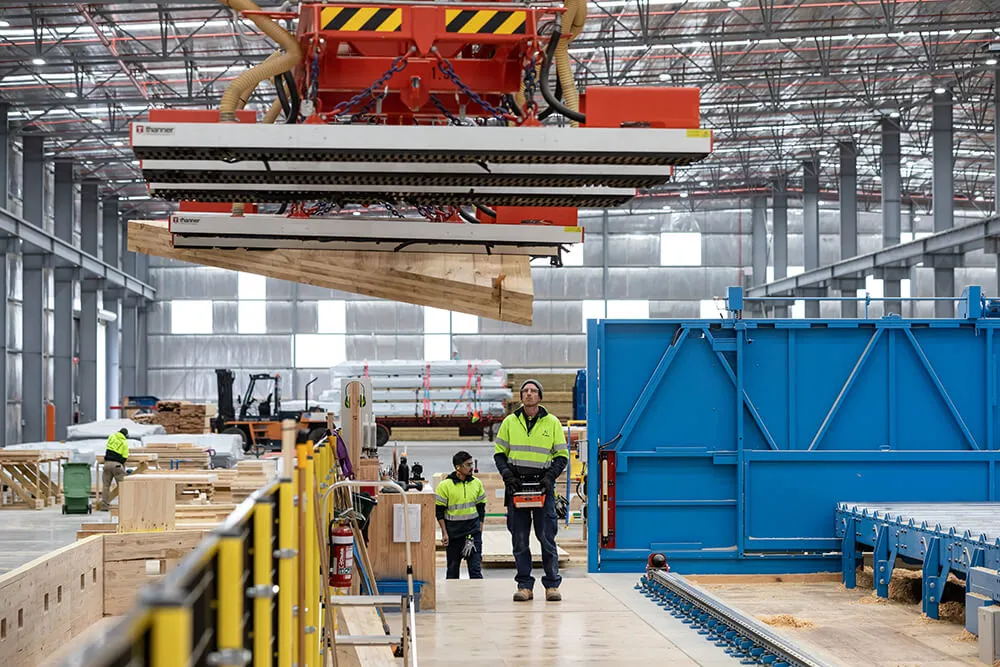
2019 — 2020
2019 started with significant investment as Hyne commissioned the expansion of their GLT plant in Maryborough. But no one could’ve predicted how 2019 and 2020 would pan out with Hyne experiencing 15 months of unprecedented salvage of 1.6 million burnt plantation pine logs, followed by the effects of the pandemic. Despite ongoing adversity, in 2020 Hyne introduced the Tumba robots, a world-first, fully automated sorting and packing production unit for graded timber.
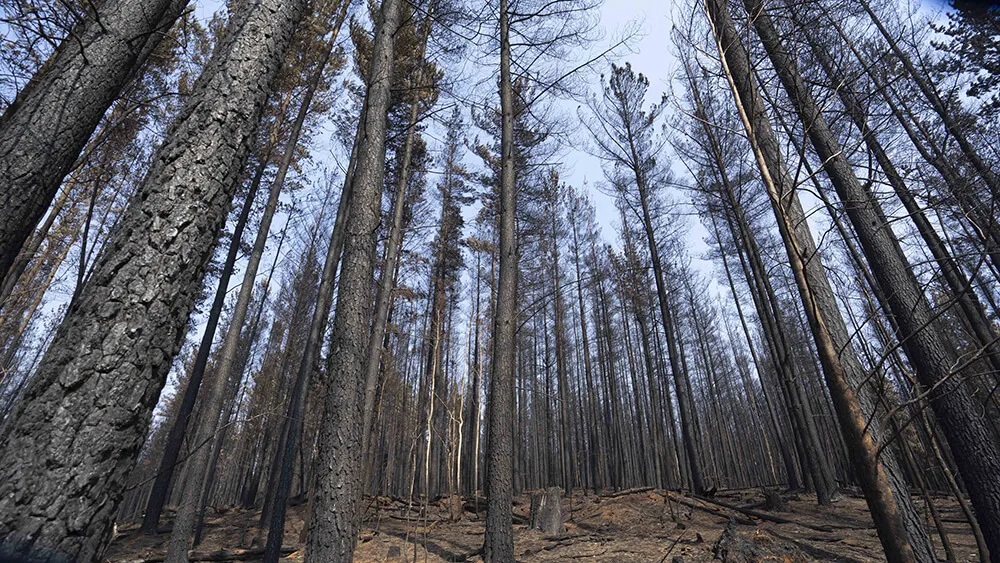
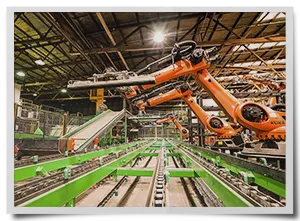
2021 — 2022
In 2021, Hyne invested $14.5million into the Tuan Mill with a new Continuous Drying Kiln (CDK). The addition of the CDK meant an increase in production that helped to better meet the needs of a booming market. Marking its 140th year, Hyne announce a partnership with UK-based sawmilling pioneer, James Jones & Sons Limited, bringing together a combined 320 years of family-owner sawmilling heritage and heralding more growth opportunities.
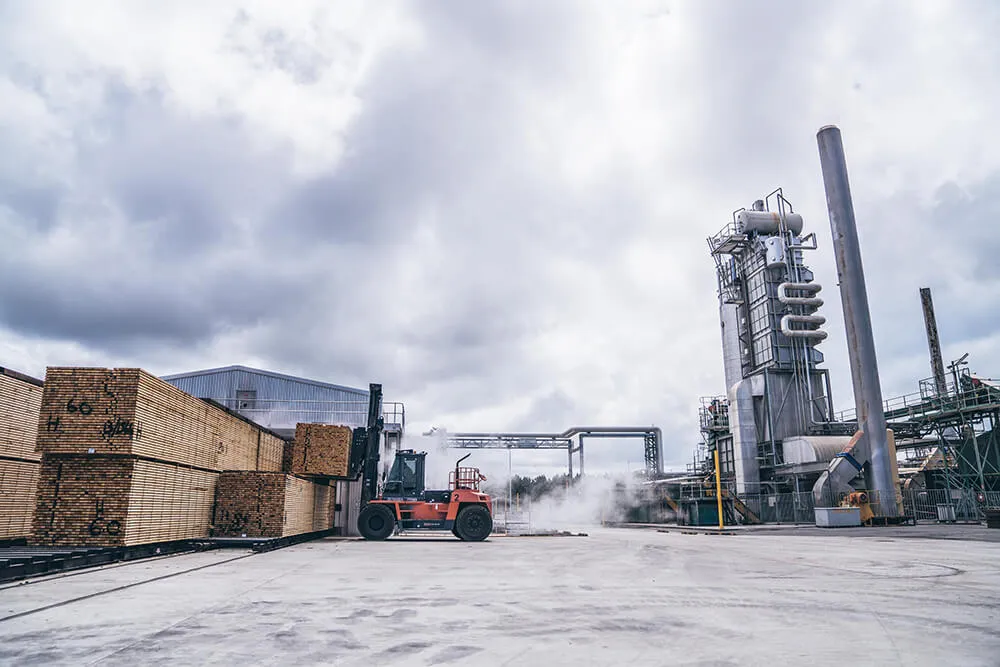
By knowing our past, we see our future
Our Company
Vision, mission, values and more
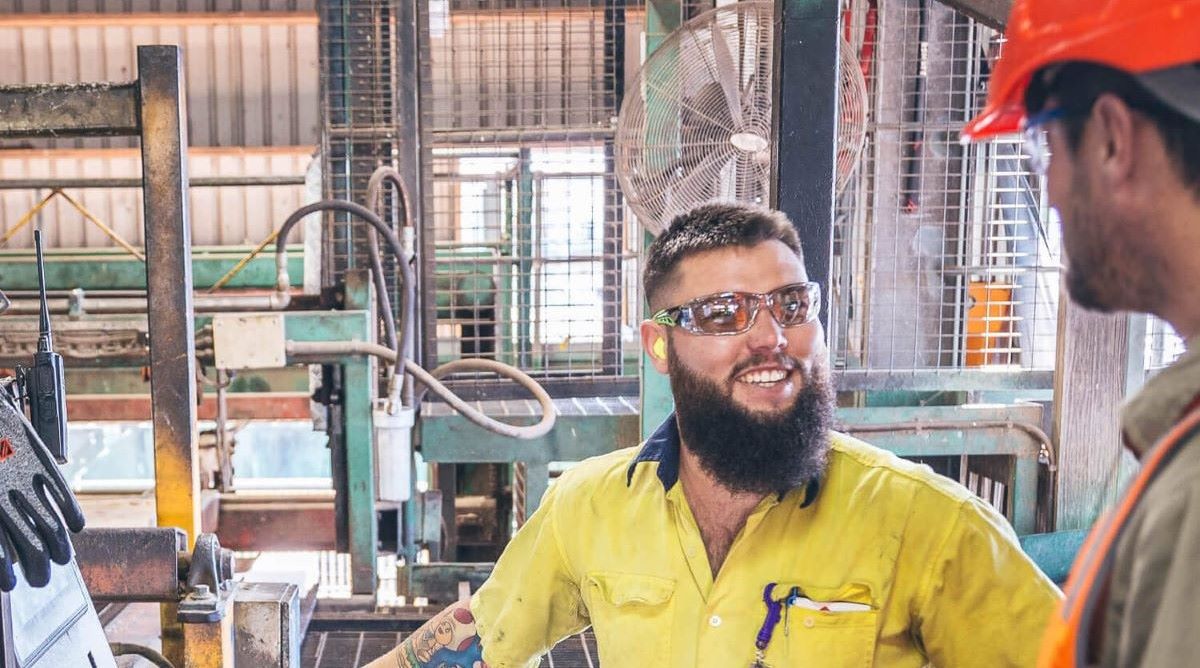
Tour a Timber Mill
Step inside our mill
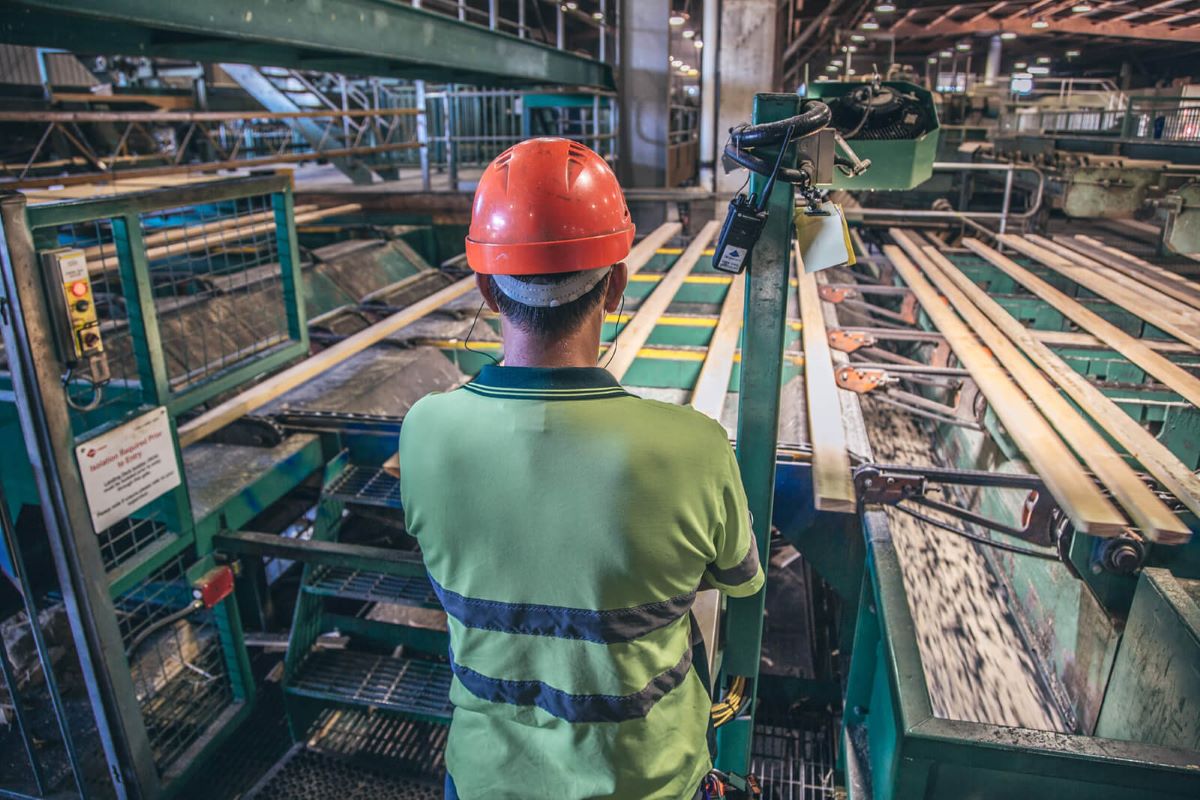
Careers at Hyne
It’s our people that make us great
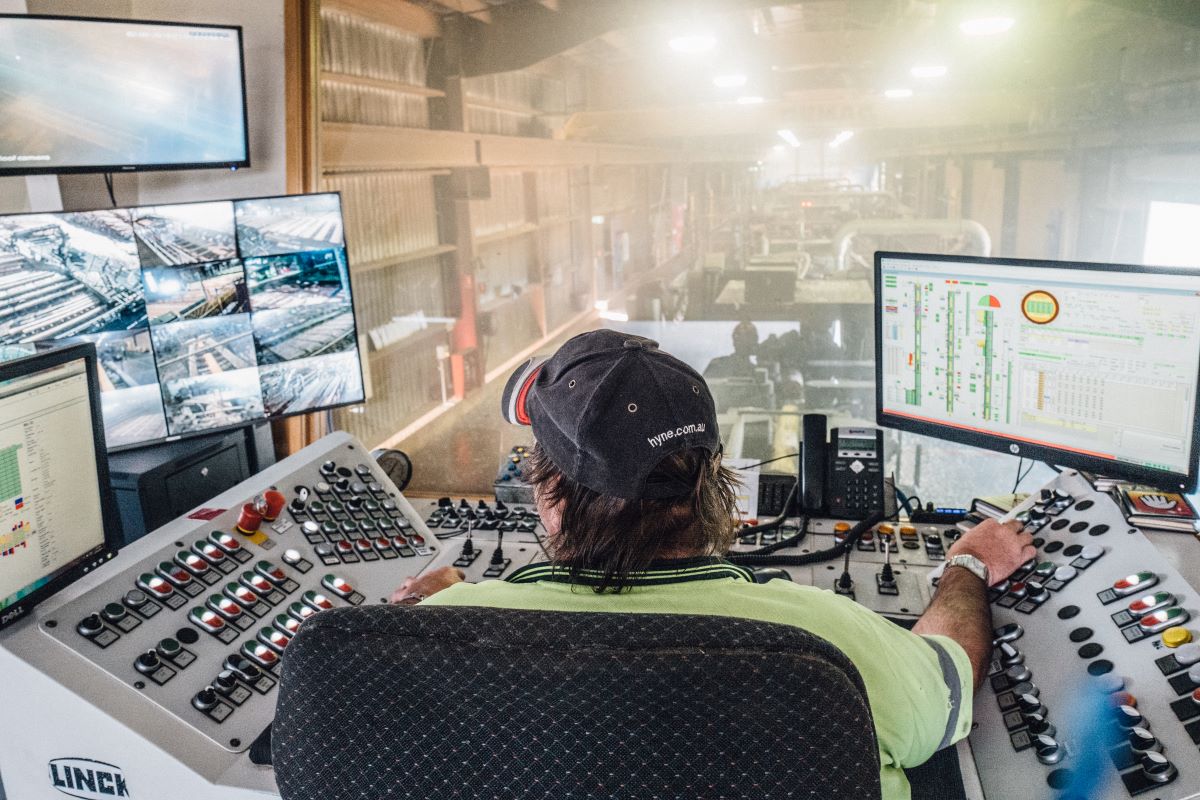
Tour a Timber Mill
Step inside our mill
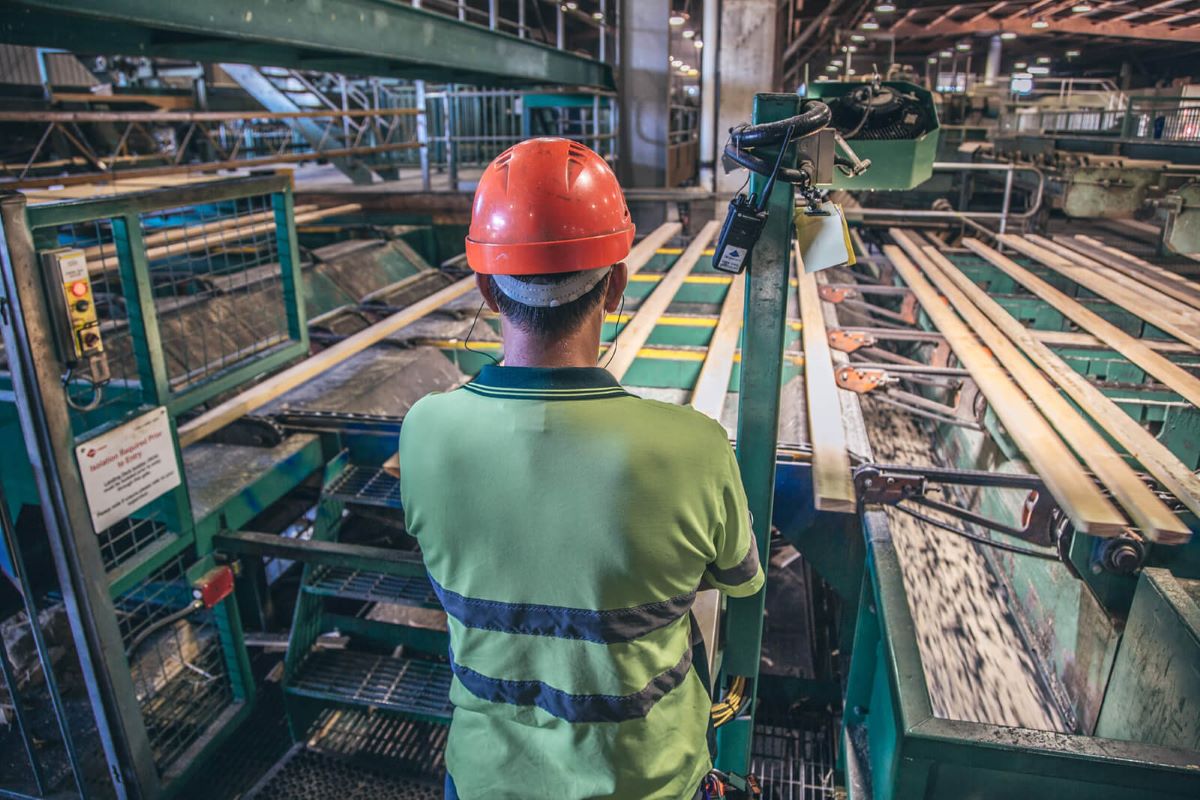