Tumbarumba Mill
The new millennium began with Hyne’s single biggest investment – the expansion of the Tumbarumba Mill in 2001, which would grow into the biggest employer and the lifeblood of the New South Wales country town; marking a conscious decision to open new markets down south.
“There were almost tumble weeds blowing down the main street at the time,” said Peter Hyne. “The town felt they’d heard it all before when we told them we wanted to overhaul the mill, which was very old and needed a lot of love and attention.”
Tumbarumba born and bred Eric Jackson-Hope, who has now worked for Hyne for 40 years, remembers the site in 2001.
“It was a dangerous place, that was one of the biggest things Hyne did to improve operations - by making worker safety a priority,” said Eric.
Around 90 per cent of the site was eventually rebuilt and there was a high-level of investment in the mill through 2003—2006 and again between 2018—2022, including robots for the Dry mill.
“We invested $180 million into that site and watched the money flow back into the local community through the Hyne Community Trust,” said Peter Hyne. “You go there now and it’s an amazing little town that’s bustling.”
Queensland Sales Manager Jeff Gibson credits the Tumbarumba operations with taking Hyne from a mid-size to large sawmill operation.
“It was a massive project, but if we didn’t do something like that Hyne Timber may not be here today,” said Jeff. “You need to continue to grow and expand to survive.”
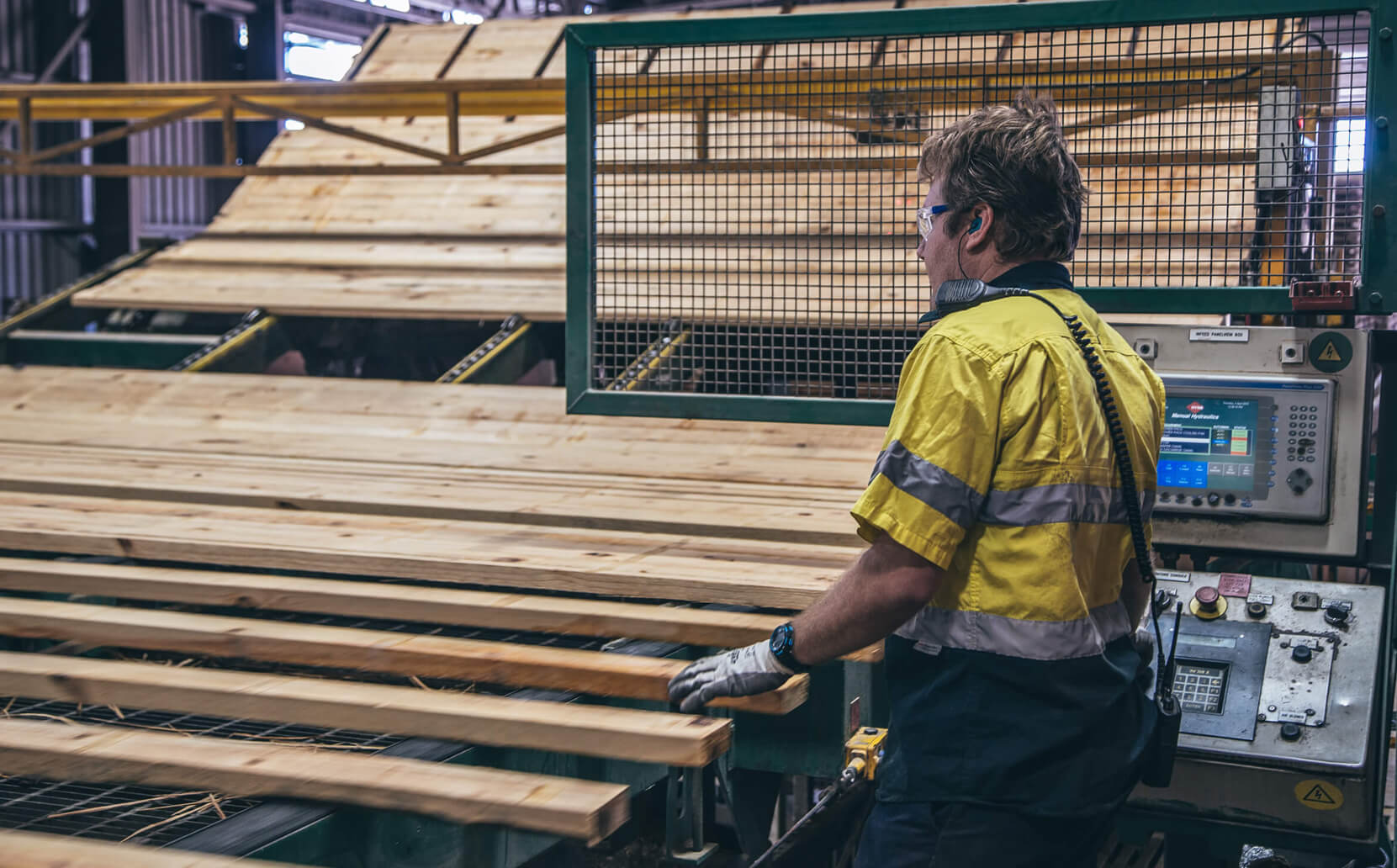
An exit from hardwood
In 2006, following the move away from logging on K’gari, Hyne’s hardwood operations were taken up by the Queensland Government, and, after 18 months managing the operations for the government during the handover, 2007 marked the company’s final exit from hardwood as the business transitioned exclusively to plantation softwood pine logs.
To replace this part of the business, Hyne saw an opportunity in how treatment of structural framing improved the durability and repelling of wood destroying insects and so began a campaign to convert the markets of Queensland, New South Wales and Victoria to treated timber.
Again, Hyne was told it could not be done while many in the market were still coming to terms with the idea that softwood timber could be used as structural framing, having always used other products, such as cypress pine and hardwood products.
Hyne stepped up with the solution, developing a world-first, low-cost, in-line treatment system at its mills.
By 2008, 30 per cent of Hyne’s structural framing sales were converted to treated T2 Blue and T2 Red. The final push to convert remaining markets to treated framing would be long and challenging.
Global Financial Crisis
The Global Financial Crisis (GFC) of 2008 dealt another blow to the business and was one of the biggest threats Hyne Timber ever faced. Again, tough decisions had to be made.
To make matters worse, leading into the GFC, Hyne had heavily borrowed to refit the Tumbarumba Mill and was highly leveraged when it hit.
“In the middle of the GFC, the price and demand for timber also plummeted,” said Martin Kriewaldt. “That was the closest we came to insolvency and it took some years to recover, with no dividends paid on Hyne shares for a decade.”
Tight financial times meant the business could no longer travel overseas and fell behind in technology – something that always set the business apart.
“The first thing we did when our finances returned was to send the engineers overseas to look at the new technology,” said Martin.
To get the business safely through, management set about shutting or selling parts of the business that were no longer profitable, including warehouses, mills and product ranges. Unfortunately, this also saw the loss of around half of all employees in the business.
“We let a fair chunk of the business go, but it was the right decision financially and has made us a simpler business to run with less risk,” said Peter Hyne.
The focus on core business also affected wholesale distribution centres, and many were closed, eventually leaving only Newcastle, Brisbane and Cairns to serve the eastern seaboard.
This period also coincided with a drastic slowdown of new houses being built, as well as a high Australian dollar leading to increased import threats.
Demand for timber is closely linked to the ups and downs of housing market cycles.
XLam – an emerging market
In 2015, the business looked to embrace another form of engineered timber: cross laminated timber (CLT) which consists of large structural building panels made from solid timber boards laminated together in cross layers to form billets.
Hyne saw an opportunity for the use of softwood timber to create higher-end product in CLT. There was no clear market in Australia at the time, but the business saw the popularity overseas and believed ‘the time was right’.
%2520(2)%2520copy_Optimised.jpeg)
A partnership with New Zealand’s XLam (founded by brothers Ian and Robin Jack in 2010), the leading provider and first manufacturer of CLT in the Southern Hemisphere, was formed.
Now wholly-owned by the Hyne Group and a sister company to Hyne Timber, XLam leads the Australian market in mass timber and has grown into a significant operation over the last decade.
The business includes sites in Australia and New Zealand, as well as a $50 million investment to establish Australia’s first CLT plant in Wodonga, Victoria.
XLam General Manager Shane Robertson also highlights the material’s environmental credentials, saying: “XLam CLT is made from renewable plantation timber, and the prefabricated nature of CLT improves safety and efficiency on site, improves construction ROI and helps to create greener buildings.”
In a move that would surprise many 20 years ago, Australia’s first mass engineered timber fire station, or as it is officially known the North Coast Regional Headquarters and Maryborough Fire and Rescue Station, has been built in Maryborough where Hyne began, from cross laminated timber in recognition of the sustainability and fire performance qualities of CLT and its many other benefits as a construction material.
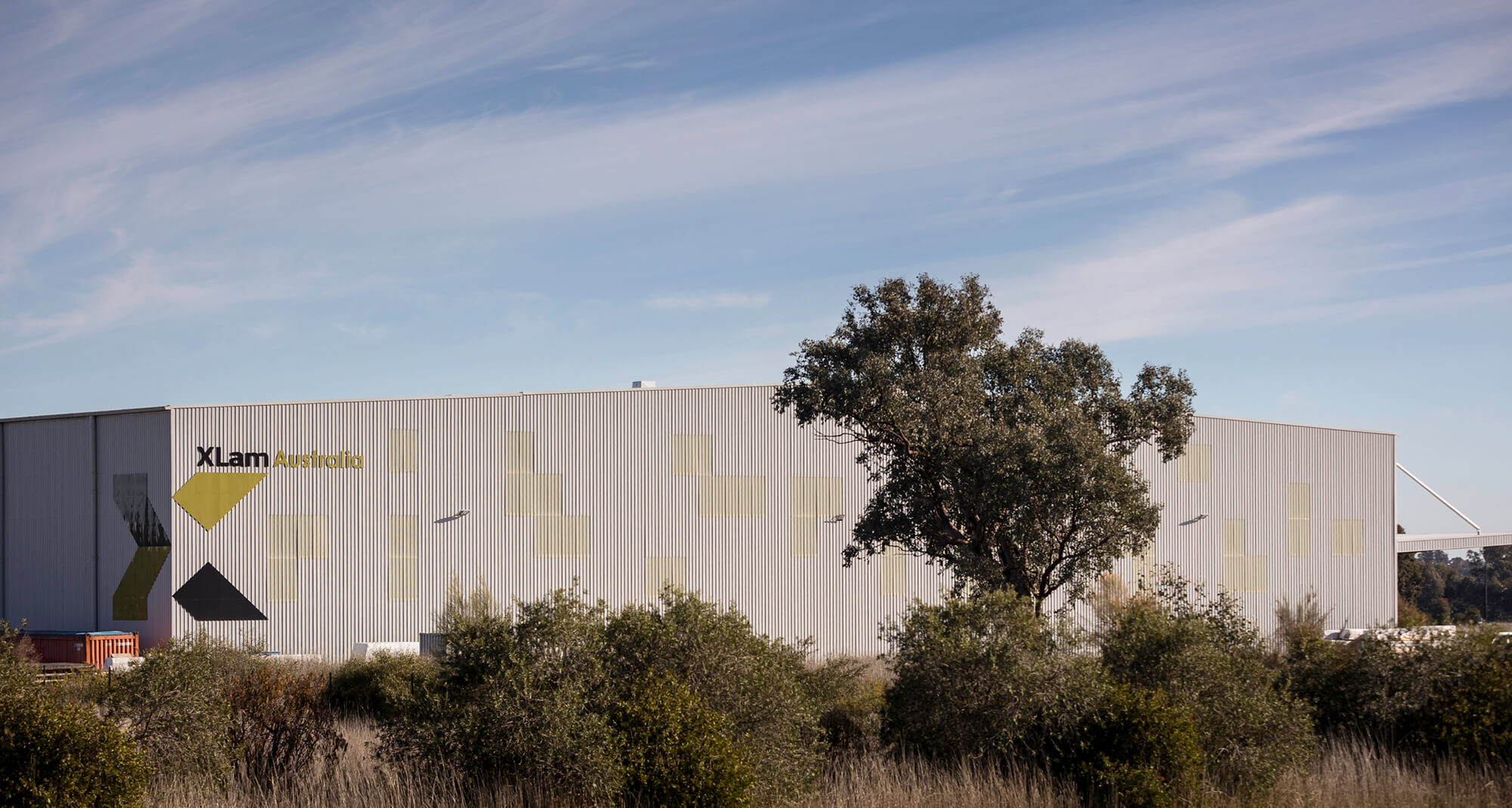
Queensland Business Leaders Hall of Fame
In 2015, the Honourable Dame Quentin Bryce AD, CVO, former Governor General of Australia, officially inducted Hyne Timber into the Queensland Business Leaders Hall of Fame, which aims to celebrate, record and retell outstanding stories of business achievement. Hyne Timber was inducted in recognition of the Hyne family’s significant contribution to the timber industry, regional employment and the innovative production of timber products for over 130 years. Accepting the award at the 2015 event was fifth-generation family member Peter Hyne, fellow Board members, family shareholders, senior leaders and retired, long serving team members. In his acceptance speech, Peter acknowledged the award as a true honour for the Hyne family. But more importantly, he stressed that this award was also recognition for team members.
“Since the company’s beginnings in 1882, my family have always acknowledged that our employees are the most valuable asset. Not mills or machinery, but the people of Hyne Timber,” said Peter. “It is our employee’s dedication and hard work, which in turn, significantly contributes to Queensland’s economic and social development.”
Mother Nature strikes again
The ups and downs of the timber industry continue in the modern day, including the 2019—2020 bushfire emergency, which saw 15 months of unprecedented salvage of 1.6 million burnt plantation pine logs.
Fortunately, Hyne’s Tumbarumba Mill was saved as critical infrastructure thanks to the many volunteers and emergency services who protected it, some who were also Hyne team members.
As CEO Jon Kleinschmidt said to staff at the time: “There is a long road ahead, but together we can rise again.”
The salvaging of burnt logs was prioritised following the emergency and once the burnt bark was removed, the structural grade timber was the same quality that customers had come to value.
“We saw resilience of the timber, resilience of our company and people, as well as resilience of the local communities impacted by the bushfires,” said Jon.
By May 2021, the last of the burnt logs were processed at the mill. The linear metres of this sawn timber (75.5M) means these logs would almost twice wrap around the world.
In between the 2019—20 Black Summer bushfires and the last burnt logs being processed, there was another challenge to navigate when, in March 2020, the COVID-19 global pandemic had reached Australia.
Despite predictions of a devastating slowdown in activity, the Government stimulus, continuing construction, and reduced volumes of imported timber – as well as the popularity of home renovations through pandemic lockdowns – saw the timber industry face unprecedented demand.
Pandemic milestones
In August 2020, six months into the pandemic, Hyne opened its new glue laminated automated timber plant in Maryborough.
This investment was enabled and accelerated by a Queensland Government Jobs and Regional Growth Fund grant.
And the new plant could not have come at a better time as renewable, Australian building materials sourced from within a secure supply chain that created and supported local jobs, became more important than ever.
Another milestone came in June 2021, when Hyne was able to announce that 100 per cent of the structural framing it manufactured was now sold into the Australian market as a treated product, building on a hunch from 20 years earlier about the treated timber opportunity.
Hyne Timber once again went against the grain and now there is no untreated framing leaving a Hyne mill or distribution centre and the industry refers to termite treated products generically as “T2”, just as Hoover is synonymous with vacuum cleaner.
“We stuck to our strategy in recognising that treated softwood framing is a product of the future as an economical and environmentally sustainable resource,” said Peter Hyne when making the announcement.
Another step forward came in October 2021 when the much-anticipated Continuous Drying Kiln (CDK) began operations at the Tuan Mill, adding around 60 additional team members at an investment of $14.5 million.
Peter Hyne says it’s the way of the business to invest profits back into the business: “In our industry, if you don’t upgrade, you won’t survive – that’s always been one of our strong points.”
The launch of the CDK coincided with the 35-year anniversary of the original installation of kilns at the Tuan Mill, which now employs around 300 people and is one of Australia’s largest suppliers of softwood framing.
The Hyne Group of businesses, including Hyne Timber and XLam, today employs more than 800 people at 12 locations on Australia’s eastern seaboard stretching from Cairns to Melbourne, as well as the glue laminated timber plant in Queensland, and XLam operations in Australia and New Zealand.